By Vicki Prichard
NKyTribune reporter
Back when Dan Togergte , president and CEO of NKY Tri-Ed, was learning the business of economic development, he came across a University of Oklahoma professor at a training seminar in Texas who cautioned him about manufacturing.
“He said, “Hey, don’t focus on manufacturing when you go back to your communities. You’re not going to do very well if you focus on manufacturing. It’s not going to work because it’s all going off shore. It’s not going to work here in the states. Service is where you want to go, we’re going to be a service economy. You’ve got to do it,”” recalls Tobergte.
Today, Tobergte says he’s glad he didn’t heed that counsel.
“Ever since, we’ve done target industry analysis and have had consultants come in and they have validated each and every time that all the ingredients for successful advanced manufacturing are here within this region,” Tobergte told guests at the Covington Business Council (CBC) luncheon this week at the Madison Event Center, where a panel addressed the critical role of securing a skilled workforce for the industry.
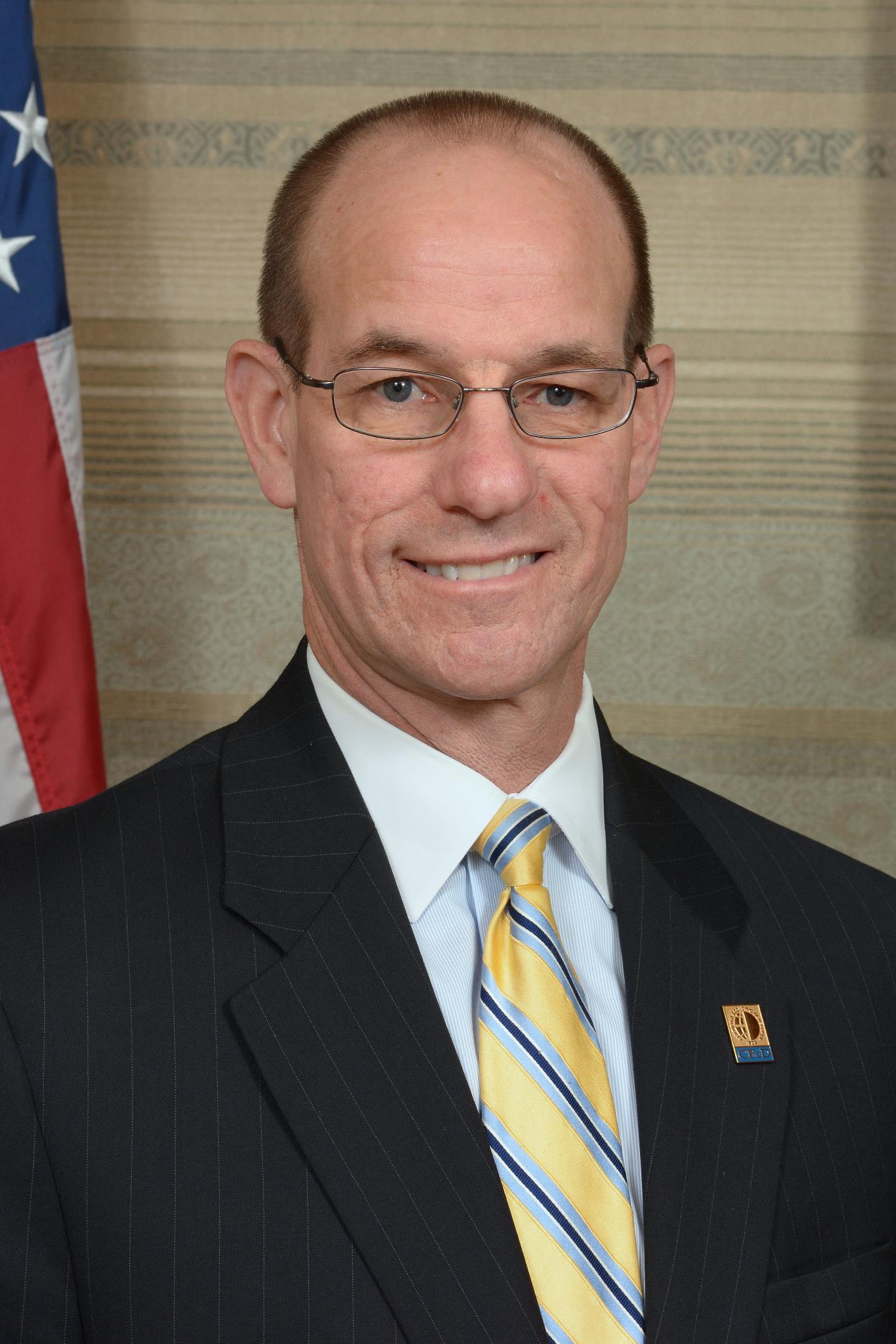
“Advanced manufacturing has been Northern Kentucky’s bread and butter,” says Tobergte.
Last year, among primary industries in the region, 12 projects were announced, involving expansions or new locations. That growth, says Tobergte, outpaces state and national growth.
“Almost 21,000 jobs are directly involved in manufacturing in Boone, Kenton and Campbell counties,” says Tobergte. “We have a 23 percent growth compared to 6.8 percent nationally.”
Dialing it down to one city, he says Covington has seen a 14 percent growth in manufacturing, with the average earnings of workers at $82,000.
“That’s quite strong to the testament that we have a very strong industry base here in Covington to explore,” he says.
Steve Barnett, owner and CEO of Indy Honeycomb in Covington which manufactures a product that serves the purpose of the seal inside a jet engine, says he moved his business to Northern Kentucky because it was “home,” but that other key factors played a role.
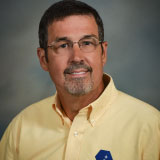
“Here we’re close to a lot of suppliers, close to the airport, there are good roads, good schools available — both high schools as well as colleges — so that was good for our employees,” says Barnett.
But finding good employees has been an issue for the manufacturing industry.
A 2012, a Northern Kentucky Industrial Park (NKIP) study showed that there were about 680 unfilled positions in the region, and projected that over a ten-year period the numbers were going to increase, says Rhonda Whitaker, Duke Energy community relations manager for Kentucky. In response, the Advanced Manufacturing Workforce Development Coalition was formed in 2014 to help develop a talent pipeline for current and future job needs within the manufacturing sector in Northern Kentucky. The coalition came together in a collective impact approach, bringing organizations together that were trying to achieve common goals for large scale change around filling the talent pipeline.
“When Dan talks about the strength of the economy around here for manufacturing,” says Whitaker, “it is very strong, but we have to keep in mind that we want to continue to attract manufacturing here because it is good of your economy and we want to make sure that businesses that are here remain here.”
She says it was evident from the NKIP study that manufacturers were saying workforce development was something that warranted attention.
“Our coalition really set out to move the needle on how we could fill those jobs,” says Whitaker.
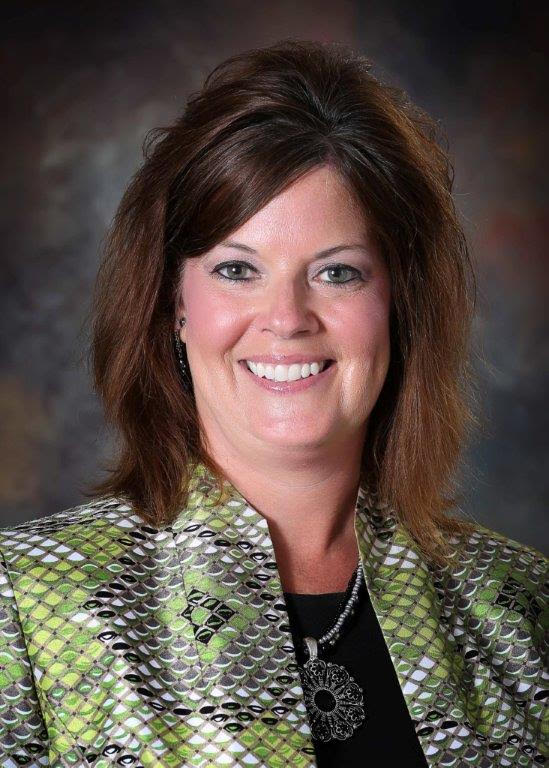
The coalition is constructed with a backbone organization called Partners for a Competitive Workforce which is managed by the United Way.
“They are really the regional umbrella organization for workforce development in the tri-state region,” says Whitaker.
Whitaker and Mazak’s Mike Vogt co-chair the effort, along with a number of manufacturers who serve on the coalition.
“We’ve recruited eight to date and have a few more in the pipeline,” says Whitaker. “We want this effort to be an employer-led effort.”
Last year they hired Ed Ratterman as a director on a contractural basis. They have many other partners including Impact Northern Kentucky, the impact arm of the Northern Kentucky Chamber of Commerce, Tri-Ed, Skyward and Gateway Technical and Community College.
Among the coalition’s elements is the ad campaign, I Made it NKY, which was initially directed at millennials, trying to drive them into interest in the manufacturing sector. When they tap on links related tonkbthe I Made it NKY ad, they are directed to training opportunities at Gateway with its Advanced Manufacturing Center. The next piece of that campaign, she says, will not only send them to training opportunities but will also be linked to job openings through the Kentucky Career Center.
The coalition is also working in high schools, training and preparing youth and adults.
“The Kentucky Fame program was something that a chapter was formed here from the program Toyota started years ago in Georgetown,” says Whitaker. “A chapter was formed here by local manufacturers who worked with some of the coalition partners.”
Kentucky Fame, the Kentucky Federation for Advanced Manufacturing Education, is a partnership of regional manufacturers which implements dual-track, apprenticeship-style training to create a pipeline of highly skilled workers. It presents the opportunity for an individual who goes through the program to basically get paid work and experience while training at Gateway for an Advanced Manufacturing Technician (AMT) certification.
Whitaker says that program addresses what the NKIP identified as the second most in-demand position in Northern Kentucky, which is maintenance technician.
The coalition looked at the top most in-demand position, enhanced operator, and started facilitating discussions among manufacturers and Gateway to come up with curriculum and core competencies to address that position and developed the enhanced operator program — a 16-week course, of which 70 percent can be completed online.
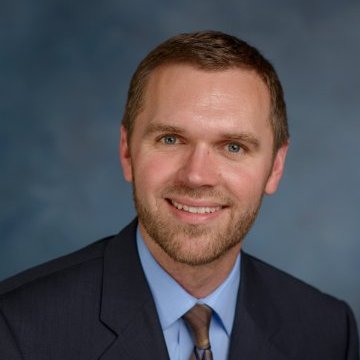
Whitaker says they’re also looking to update demand data as they move forward to understand the needs of area manufacturers, as well as advocacy effort to see what can be done about state and federal legislation that might have some kind of impact for workforce needs.
Josh Benton, executive director of the workforce development division with the Kentucky Cabinet for Economic Development, who joined Whitaker and Barnett on the panel, cited signifiant momentum around manufacturing in Kentucky.
Last year alone, there 450 new projects in Kentucky from new locations or expansions within the state.
“That’s a significant amount,” says Benton. “It was nearly five billion dollars worth of private investor dollars in the state. When you look over the last two years combined, 2014 was a record year for private investment in Kentucky, and we eclipsed in 2015.”
Benton says Kentucky is fifth in the nation when it comes to manufacturing GDP, with seven regions in the state that saw growth in employment — four of them above the national average. Those regions include Louisville, Lexington, Bowling Green and Hopkinsville, and Northern Kentucky.
With that growth, says Benton, comes some workforce issues.
“We’re a relatively small state in terms of population and one of the biggest issues that we face is our labor force participation rate,” says Benton.
Coming out of the recession, he says, they saw increased baby boomer retirements, and people who gave up on their job searches. He points out that the recent increase in unemployment actually means more people are beginning to look for employment again.
“That’s a good thing,” says Benton. “They’re submitting applications and re-entering job searches. We have a 53.4 percent labor force participation – we’re 47th in the country. That causes a mismatch of supply and demand.”
Benton noted that the recent Lane Report saw dramatic increase manufacturing in Kentucky.
“The growth is phenomenal but we have to have skilled people to fill those jobs and maintain our growth and still be attractive to new companies,” says Benton.
Kentucky Fame, he says, is a statewide phenomenon over the last year and a half, with Northern Kentucky part of the second wave of chapters in the public/private industry-led partnership.
“We currently have 58 companies sponsoring 150 students at the AMT program,” says Benton. “Starting in the Fall of ’16, we expect the number of companies to increase to 130, with 250 new students in addition to the ones we already have. The key to this is that it is industry-led — you have educators at the table, government at the table — talking about what the demands are; education and government aligning resources to meet those needs.”