By Mark Hansel
NKyTribune managing editor
The panel at the April Northern Kentucky Chamber of Commerce Eggs ‘N Issues discussion represented the diversity that is a hallmark of the region’s business landscape. Despite their different business models, however, all of the companies have one thing in common – automation is vital to their success.
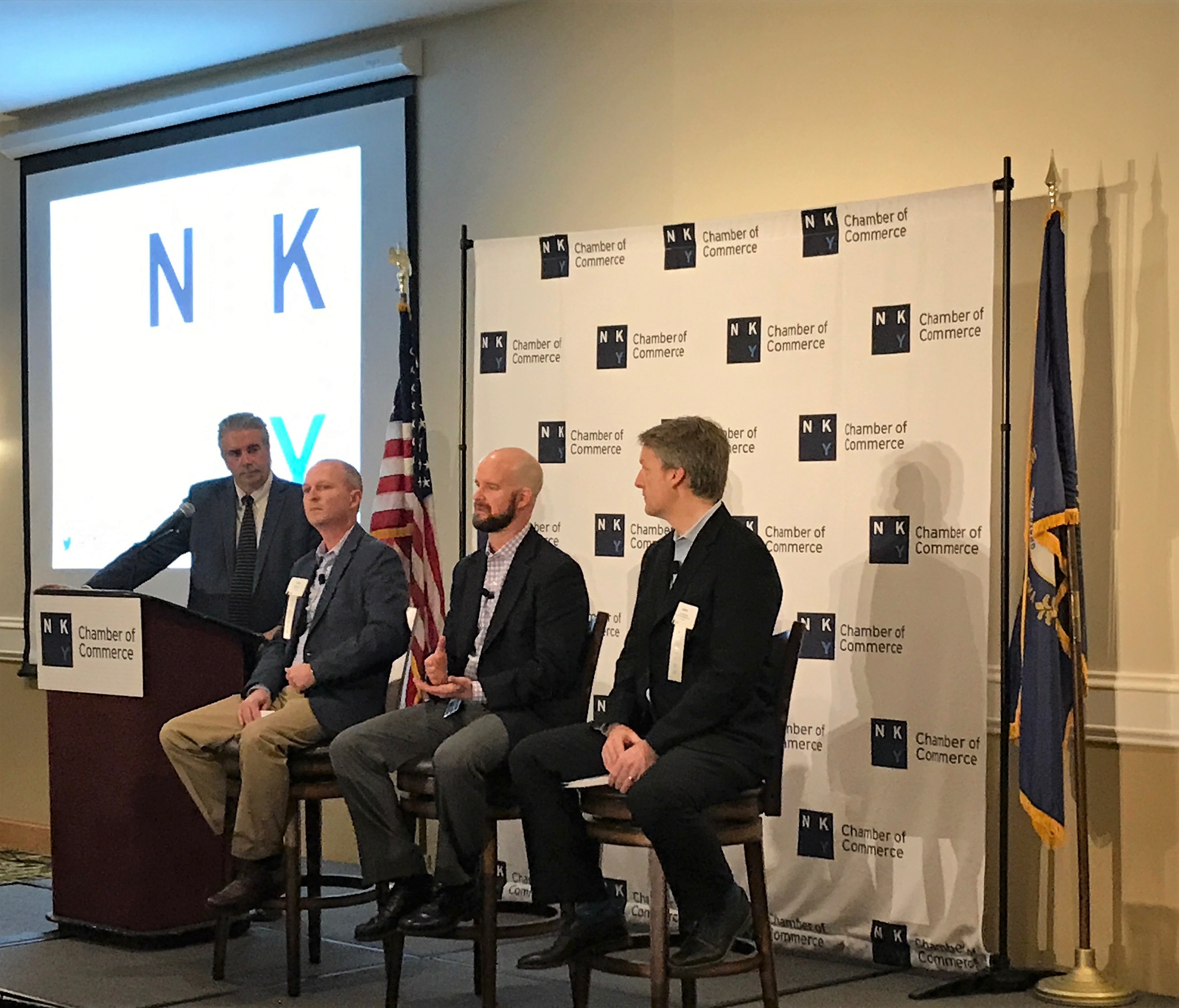
Panelists John Baines, president of HAHN Automation North America, James Biro, vice president of supply chain, at Perfetti Van Melle and Kurt Cheek, director of operations for iHerb, spoke to how the topic, “NKY is Embracing Automation,” applies to their respective business models.
iHerb is a direct-to-consumer fulfillment company, for vitamins, supplements, health, beauty and all-natural products. It has facilities in Hebron, and in Bristol, Pennsylvania.
Cheek said at iHerb, the first thing that comes to mind is people.
For us, it was looking at, if the company was balancing our people with what we need to exceed customer expectations and that was the big drive,” Cheek said. “We weren’t looking at automation to replace people, we were looking at automation to exceed customer expectations and the automation we currently have in our Hebron facility allows us to do that. The other piece is it allows us to be more efficient in our operation with our people in other areas of the business.”
Perfetti Van Melle is a global manufacturer and distributor of confectionery and chewing gum located in Erlanger.
Biro said the focus is not only how does automation make the company more efficient but how does it also raise the level of the jobs that are being done.
“When you can automate something that’s a very basic job,” Biro said. “The goal is to keep that job for someone doing a higher-level integration, or analytics, or troubleshooting. Then your whole business gets stronger.”
The challenge then becomes finding people capable of filling those positions.
“We’re seeing a changing in tying less effort into repetitive jobs, work and tasks, and trying to elevate it into how do we have people liberated from that job, so they can focus on higher end tasks,” Biro said. “The biggest challenge that we have right now, is that the skill level has changed drastically, so now we see a gap where you can’t find enough people.”
Hahn Automation is a German-based custom automation company located in Hebron. Its customers include automotive parts suppliers, medical device makers and consumer goods manufacturers.
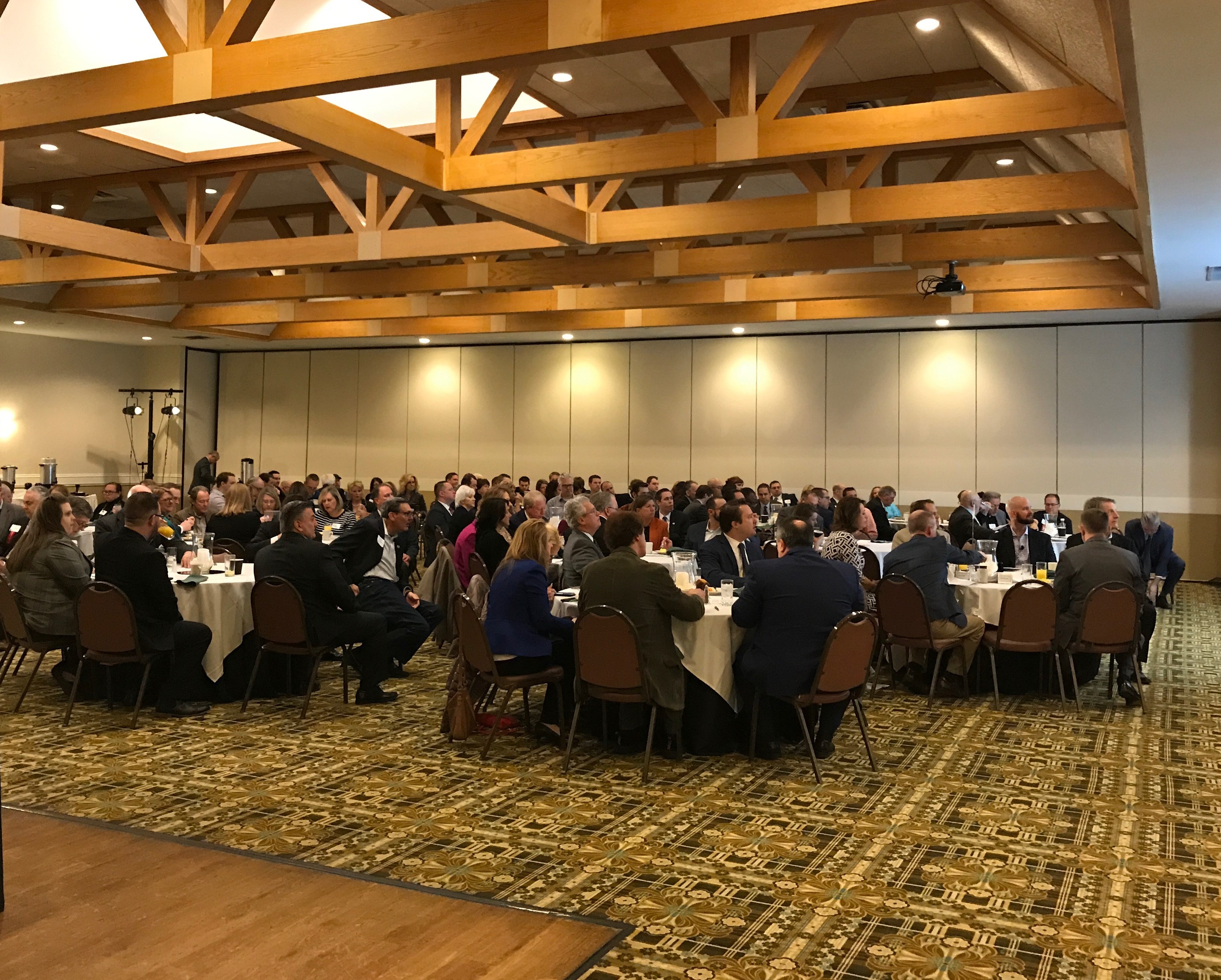
Baines says that while Hahn is an automation provider and manufacturer, the challenges are similar.
“I would break down the impact of automation in the workplace in the same kind of category,” Baines said. “One being the shift of work to being more complex, so you are seeing a change from having a lot of operators, to having more leads or processor engineers. So hiring qualified people to run production is more difficult than hiring someone off the street with no training.
The other side of that is, there is a lot more information available in production that allows Hahn to make more informed decisions about how to improve the process.
“The one that really gets overlooked that’s very important, is that the level of safety has improved,” Baines said. “We talk about replacing people, but there’s a lot of areas where you want to replace people. You don’t want people doing dangerous jobs. Dangerous work, whether that simple ergonomics, or truly hazardous work, can be automated by machines to improve safety.”
Artificial intelligence has been an automation buzz-phrase for some time, but it has also evolved. No longer are customers just calling in and, “Saying 1 to speak to an operator.”
“Imagine the point at which artificial intelligence gets to the stage where you can write an algorithm that takes over your whole customer service,” Biro said. “So, suddenly it’s not only, ‘I’m selecting where to go with my voice,’ it’s decisions that are being made or documents are being read or consumer complaints that are being identified. There is an algorithm behind it that starts making the decisions that some employees do today. So, it goes from automating putting something in a box to automating decision making.”
At iHerb, artificial intelligence contributes to both the customer service side and the production effort.
“What we’re focusing on now is to try to determine what you’re going to order based on your ordering pattern and then, can I do something in the facility that allows me to be more efficient,” Cheek said. “We’re not there yet, but that’s one of the things that we’re looking at to determine, ‘If I’m ordering toothpaste, am I ordering shampoo with it, or am I ordering vitamin C,’ for example.”
On the production side, iHerb has developed the Perfect Pick system, which allows it to store about a million units in a footprint that takes up minimal space.
“This piece of equipment, from a customer experience perspective is about 99.99 percent accurate in terms of our processing and speed to customer,” Cheek said. “That allows us to ship a customer order within 30 minutes of the time it is placed.”
In Hebron, iHerb employs about 300, but just 25 people in processing. The system automation allows the company to process about 20,000 orders a day, consisting of 120,000 units in a 10-hour shift.
Baines said one of the automation trends Hahn is seeing is direct machine and human collaboration or collaborative robots, but that’s just one innovation.
“There are new products on the horizon, where we can look at something that’s going on and get it to our customers,” Baines said. “They can get information directly about our specifications, they can talk online to our CERF technicians and see what the machine is supposed to be doing. Yes, it’s more complex in general, but I would also say that…certain things will become much easier, while we are pushing the frontier to do things that are even more complex.”
While a skilled workforce continues to be a burden in advanced manufacturing, finding long-term employees is also a problem for jobs that don’t require as much training.
“We are still looking for people that want to work, not for people that need a job and in Northern Kentucky that’s a tough challenge,” Cheek said.
Despite the promise of steady employment, many employees bolt when distribution companies that hire seasonal workers advertise a higher starting wage.
The panel agreed that, in a highly competitive business world, continued automation in the workplace is necessary across all industries.
The world is not going to get less complex and the quality of work, the challenges of work, and the opportunities in the future will continue to expand.
The Eggs ‘N Issues discussion takes place monthly at Receptions Banquet and Conference Center – South in Erlanger. For more information on Eggs “N Issues and other NKY Chamber programs and events, click here.
Contact Mark Hansel at mark.hansel@nkytrib.com