Abrasive wheel grinders are like the Swiss Army knives of the manufacturing world. They’re everywhere, especially if you’ve got a mechanical or maintenance shop onsite. But, just like any other piece of equipment, if you don’t check and maintain them, or use them incorrectly, they can cause some serious injuries or even deaths.
There are a ton of different types of grinders, including bench grinders, pedestal grinders, angle grinders, and more. It’s like a grinder party! No pun intended.
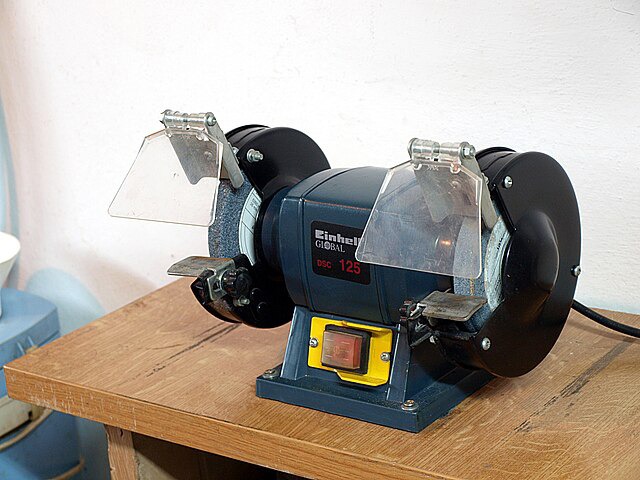
The two more common grinders I run across in an industrial or commercial setting are bench grinders and pedestal grinders; and both do basically the same job. The trouble that I find on a regular basis is that many of these are missing guards, not set up correctly and are not properly maintained. What is even concerning is that according to an OSHA review of 27 grinder accidents in an eight-year span, more than 26% resulted in employee deaths.
Usually when I point this exposure out to a client, their first reaction is to roll their eyes, chuckle or to just give me that look like I’m nitpicking. But then when I tell them that people have been killed while operating these grinders, I quickly get their attention.
Accidents often happen when employees get their clothing, employee badge, jewelry, fingers, or other body parts caught in a grinding wheel or when they’re struck by debris from an exploding or disintegrating grinding wheel. Finger and thumb amputations are extremely common, making it feel like a horror movie, but with grinders.
The grinders we’re talking about here are usually mounted to a workplace bench or pedestal with two grinding wheels used to sharpen hand tools or grind other materials like metal. The grinding wheels are made of ceramic material and spin at high speeds, typically up to 3,600 RPMs. People can get hurt, badly when those wheels become cracked, or protective guards are loose, missing, or not adjusted properly. It’s like playing with fire, but with ceramic wheels.
Safety measures are crucial to prevent these costly and painful incidents. These accidents are easily avoided through equipment maintenance and training. Regrettably, people become complacent about grinder hazards or just don’t know how to inspect and keep them safe. I often find grinders that are out of spec and could easily cause an injury or fatality. People using these machines need training, and we need to make sure that they get it. It’s like teaching someone to ride a bike, but with more sparks.

OSHA provides a checklist for abrasive wheel equipment grinders that, if abided by, can dimmish and avert deaths and serious injuries. Here’s a brief overview of some safety guidelines that can be integrated into ongoing inspections.
• Do side guards cover the spindle, nut, and flange 75% of the wheel diameter? To prevent injuries when a wheel disintegrates, ensure that side guards cover the spindle, nut, and flange at least 75% of the wheel diameter. This containment will keep the pieces within the guard, preventing them from flying around and hitting the user or others nearby.
• Is the work rest used and adjusted to within 1/8-inch of the wheel? This helps prevent items like shirt sleeves, jewelry and other objects from being worn from being pulled into the wheel and ensures that objects don’t flip up and hit the user in the face.
• Is the adjustable tongue guard on the top side of the grinder used and kept to within 1/4 inch of the wheel? The guard must be positioned within a quarter inch of the wheel to effectively contain any pieces if the wheel disintegrates. Additionally, it helps to contain sparks, ensuring a safer working environment.
• Is the maximum RPM rating of each abrasive wheel compatible with the RPM rating of the grinder motor? It’s essential to verify the maximum RPM of the grinder’s motor and ensure that the abrasive wheels are compatible with it. Both the grinder and the wheel should have the RPM clearly marked to prevent any accidents
• Before new abrasive wheels are mounted, are they visually inspected and ring tested? Look for cracks, chips, or other signs of damage. Ring testing typically involves holding the wheel up in the air by a finger through the center and tapping it with a nonmetallic implement like a piece of wood or a plastic screwdriver handle. The wheel should make a ping sound. If it goes “thunk,” that means it’s cracked or otherwise damaged. Mark it as unusable and return it to the supplier or throw it out! It’s like playing a musical instrument, but with wheels.
Other grinder safety practices should be to maintain cleanliness maintained around grinders to prevent tripping and falling into the grinder. If used excessively, dust collectors and powered exhausts should be provided Safety goggles or face shields should always be worn when grinding.
Bench and pedestal grinders should be permanently mounted, have an individual on-and-off control switch and should have a permanent, continuous, and effective path to the ground to maintain good electrical safety. each grinder.
In most industrial and commercial sites, grinders are often overlooked until they are needed. It’s crucial to apply consistent safety measures for grinders, just as you would for commonly used equipment. Regularly check your grinders and train your employees on proper maintenance and usage to prevent severe injuries and fatalities. Your workplace safety training program should include essential courses on machine guarding, PPE, and site-specific details that reflect your equipment.
Be safey my friends.