Fatalities caused by falls from elevation continue to be a leading reason for death for construction employees, accounting for 350 of the 937 construction fatalities recorded in 2015 (BLS data). Accordingly, “National Safety Stand-Down To Prevent Falls in Construction Week” begins May 8 to focus attention on this preventable probem.
An OSHA study shows that a lack of proper fall protection remains the most frequently cited violation.
Falls from heights are the leading cause of injuries and fatalities in construction, with those coming disproportionately from small residential construction contractors. In addition to the fatalities, there are over 10,000 others that are seriously injured by falls.
The National Fall Prevention Stand-Down campaign is intended to raise fall hazard awareness all across the country in an effort to reduce and eventually eliminate fall fatalities and injuries. This campaign to Prevent Falls in Construction began in 2012 with construction industry stakeholders seeking a way to raise awareness.
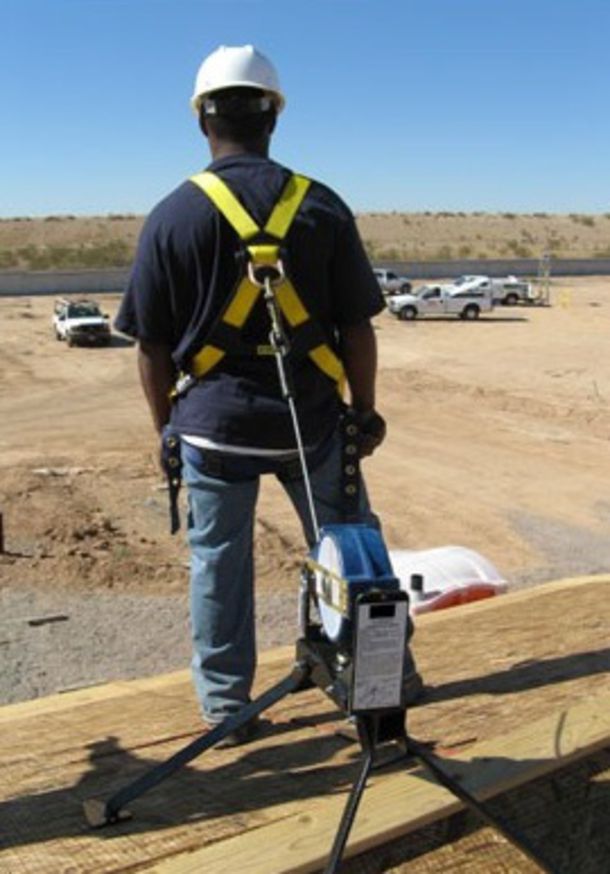
In response to the staggering number of fall‐related injuries and fatalities, OSHA, the National Institute for Occupational Safety and Health, the NORA Construction Sector Council, and CPWR – The Center for Construction Research and Training, launched the Fall Prevention Campaign on Workers Memorial Day.
The campaign is now entering its sixth year and encourages contractors to PLAN ahead to get the job done safely; PROVIDE the right equipment to workers; and TRAIN everyone to use the equipment safely year round.
I can still remember being out on a construction site in Nashville with a client conducting an onsite safety a few years ago. The project manager was very proud of his safety efforts and had bragged that he had a good handle on his fall protection requirements.
He mentioned the fact that he had assessed his fall hazards and had devised his plan, issuing out Personal Fall Arrest System (PFAS) full body harnesses and had properly trained all his employees on how to properly use them.
Shortly thereafter, a guy working some 18 feet in the air and was wearing one of these required PFAS. At first glance from a distance everything seemed okay but once we climbed up to the elevated work platform on which he was working, it was clear that there were some major safety issues.
First of all, the PFAS was being worn backwards. It was too loose and he was tied off to the railing instead of the designated anchor point.
After insisting that he come down to talk to us, we learned very quickly that the employee was a temporary worker from Vietnam and didn’t speak any English.
So despite all the confidence and countermeasures to prevent a serious injury or fatality from a fall, there could still be a communications breakdown.
The Stand-Down provides an opportunity for employers to talk directly to employees about the risk of falls, protective methods, and the company’s safety policies, goals and expectations. Companies can participate by halting work and providing a focused toolbox talk on fall prevention, conducting equipment inspections, demonstrating fall protection and procedures, or any number of other activities that educate workers on fall hazards and solutions.
According to OSHA, the Stand‐Down has been a tremendous success the last three years, reaching an estimated five million workers total. Stand‐Downs have been reported in all 50 states and internationally. The method in which employers choose to recognize the stand-down has varied from formal training, tool-box talks, handouts, presentations, inspections, emails webinars and handing out tee-shirts.
From my prospective as a safety and risk management professional, I have seen my fair share of accidents related to construction falls. But it never ceases to amaze me how employees will take short cuts when it comes to protecting themselves.
I relate it to speeding or driving recklessly in an automobile. For many us, until we have experienced that first auto accident, it’s hard to imagine what the negative consequence for our action. But after someone has experienced a nasty fall, the reality and the magnitude of the risk becomes very real. Then it’s amazing how quickly you’ll alter your behavior.
I have a high school friend that I regularly check on who experienced a life-altering accident. He was working on top of a fully-extended elevated lift while he was painting a barn.
Unfortunately the equipment on which he was standing wasn’t on solid footing and it gave way, causing it to topple and causing him to suffer several injuries. After two years, he continues to remain off work and to suffer from a debilitating major head trauma.
Such accidents occur with some regularity and these campaigns help bring additional awareness to both employers and employees.
Here is some additional information with regards to this campaign:
What is a Safety Stand-Down? A Safety Stand-Down is a voluntary event for employers to talk directly to employees about safety. Any workplace can hold a stand-down by taking a break to focus on “Fall Hazards” and reinforcing the importance of “Fall Prevention.” It’s an opportunity for employers to have a conversation with employees about hazards, protective methods, and the company’s safety policies and goals. It can also be an opportunity for employees to talk to management about fall hazards they see.
Who Can Participate? Anyone who wants to prevent falls in the workplace can participate in the stand-down. In past years, participants included commercial construction companies of all sizes, residential construction contractors, sub- and independent contractors, highway construction companies, general industry employers, the U.S. Military, other government participants, unions, employer’s trade associations, institutes, employee interest organizations, and safety equipment manufacturers.
Partners OSHA is partnering with key groups to assist with this effort, including the National Institute for Occupational Safety and Health (NIOSH), the National Occupational Research Agenda (NORA), OSHA approved State Plans, State consultation programs, the Center for Construction Research and Training (CPWR), the American Society of Safety Engineers (ASSE), the National Safety Council, the National Construction Safety Executives (NCSE), the U.S. Air Force, and the OSHA Training Institute (OTI) Education Centers.
How to Conduct a Safety Stand-Down? Companies can conduct a Safety Stand-Down by taking a break to have a toolbox talk or another safety activity such as conducting safety equipment inspections, developing rescue plans, or discussing job specific hazards. Managers are encouraged to plan a stand-down that works best for their workplace anytime during the May 8-12, 2017.
OSHA also hosts an events page with events that are free and open to the public to help employers and employees find events in your area.
Be Safe My Friends.
Keven Moore works in risk management services. He has a bachelor’s degree from University of Kentucky, a master’s from Eastern Kentucky University and 25-plus years of experience in the safety and insurance profession. He lives in Lexington with his family and works out of both the Lexington and Northern Kentucky offices. Keven can be reached at kmoore@roeding.com.