By Andy Furman
Point/Arc
River Metal Recycling shops locally. And for a good reason.
“Every organization, regardless of size or products they sell needs apparel from time to time,” said Phil Thompson, who is the Commercial Manager for River Metals Recycling in Newport. “We all have apparel needs.”
River Metals Recycling fills those apparel needs at The Point/Arc.
“We have 488 teammates across our 20 sites,” Thompson, a 25-year employee of the company says.
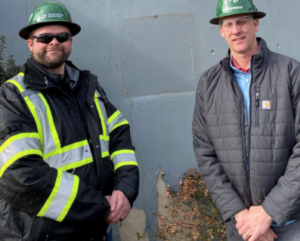
Christmas has come and gone, and those 488 ‘teammates’ found presents under their trees, thanks to The Point/Arc’s apparel shop – one of the five social enterprises offered by the 51-year-old non-profit that services individuals with intellectual and developmental disabilities – known as I/DD.
The Point/Arc creates integrated programs to give those individuals the opportunity to become contributing and inclusive members of the community and provides the self-esteem and pride that all seek.
“We certainly have options,” said Thompson, “But we decided to support The Point/Arc. It’s a local charitable organization that does great work in Northern KY.”
Thompson says if we’re getting jackets, caps, coolers, or backpacks, we’re doing it at The Point/Arc and I would encourage other organizations to consider doing the same.
Judi Gerding is the Founder and President of The Point/Arc and has been handling RMR’s company logo apparel needs for over 10 years.
RMR has been in business recycling metal at the current 10-acre Newport location over 40 years according to Thompson, who calls the process, “the beginning of the new circular economy.”
He says RMR buys end-of-life materials that would ordinarily wind-up in a landfill and helps turn that scrap metal into new products you see every day.
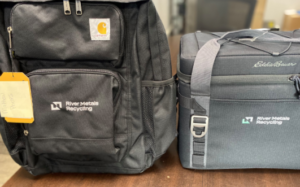
How, you ask?
“On a monthly basis, we’ll purchase approximately 8,000 cars,” Thompson said. “We take these end-of-life cars, and in about 10- seconds shred them into thousands of pieces of steel.”
That shredded steel is shipped on a barge, to a mill where it’s melted into new steel and then shipped off to manufacturers to make the next bridge, dishwasher, etc.
“All metals,” Thompson said, “can be recycled – endlessly.”
Thompson calls it, “The Circle of Life.”
The dominant method of steel production in the U.S. – called “circular steel making” – consumes up to 100% scrap metal by melting it in electric arc furnaces (EAFs). This is scrap metal that originates from local households and businesses and is accumulated and processed at facilities like River Metals. The circular steelmaking method uses significantly less energy and has one-third the greenhouse gas emissions intensity and produces only one-half of one percent of the particulate matter of traditional steelmaking using blast furnaces. Circular steelmaking also does not deplete precious natural resources and keeps material out of the landfills.
The older method of producing steel in blast furnaces – called “extractive steel making” – involves mining iron ore from the earth and refining it using a dirty process that consumes very little scrap metal and results in much higher greenhouse gas emissions than circular steelmaking, as well as other pollutants.
“We’re proud of the work our team does to support greenhouse gas emission reductions for a greener planet.” he said.